Asphalt pavement is essentially rock held together with a binder derived from the distillation of certain crude oils. Over time this binder degrades, and asphalt surfaces deteriorate.
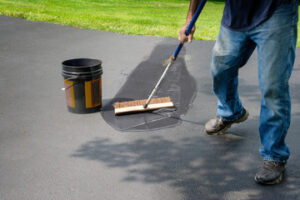
Sealcoating preserves the integrity of asphalt, extends its life, and enhances its aesthetic. It also hides small cracks, patches rough areas, and makes line striping pop. Visit https://www.rochesternysealcoating.com/ to learn more.
The preparation stage is critical to the success of any sealcoating project. This is when you protect areas that should not be sealed (such as walls, lawns, flower beds, etc), remove any oil or chemical spills, and clean the pavement surface to be coated. This should be done using air blowers, brooms, and small-bristle brushes for hard to reach spots such as crevices. The pavement must also be completely dry prior to application, so it’s a good idea to schedule this job for a day when rain is not expected or have sprinklers turned off for the duration of the work.
Pavement cracks should be filled and potholes patched prior to applying a seal coat. This is essential for proper drainage, which is key to a long-lasting and structurally sound asphalt surface. In addition, weeds and grass should be removed, as they can compete with the pavement for water and nutrients and deteriorate it quickly.
Once the repairs are complete, the parking lot should be blocked off and made inaccessible for several hours to allow the sealcoat time to cure. This should be communicated to customers and suppliers, as they may need to restock or receive deliveries at alternative locations during this time. This will also help to prevent any disruptions or delays of business operations.
During the preparation stage, the sealcoating concentrate should be mixed with sand and additives according to the manufacturer’s recommended ratios. This is to ensure that the materials are compatible and will react together in the proper manner. Sand should be screened to determine its particle size. This information is important because the gradation of sand can impact both the traction of the cured sealcoating film and the aesthetically pleasing, textured appearance of the resulting finished product. The sand should be rated for sieve size, % retained, and % passing to ensure that the correct amount is used.
During the mixing process, the ingredients are blended together to create a smooth and consistent coat that will adhere properly to the pavement. There are many different types of additives that can be included in the mix to achieve specific results. These can include modifying the drying time, altering sand suspension, increasing surface flexibility, and improving resistance to salts and petrochemicals.
Mixing
The ingredients for the sealcoat are mixed together in a specialized mixing tank or system to create a uniform mixture. This process can be done manually or mechanically and is very important for quality control. It is recommended to follow the manufacturer’s instructions for proportions and consistency.
The main ingredient in sealcoat is Refined Coal Tar Emulsion, or RTS, a black liquid that is the byproduct of coal distillation. It is highly toxic and can cause health problems for workers and the environment if not properly handled. It is recommended to use only a professional that is experienced in handling and applying this material.
Other ingredients in the mix include fillers and aggregates, plasticizers, and additives. These help to achieve the desired performance characteristics of the final product. Additives can assist in drying the sealcoat faster, altering sand suspension, increasing water repellency and flexibility, or adding resistance to salts and petrochemicals.
Once the mixture is prepared, it undergoes quality control testing to ensure it meets the required specifications. This includes a number of tests, such as viscosity, solids content, and pH levels.
Before the actual application of the sealcoat, it is important that the pavement be completely dry. This can be accomplished by sweeping and/or blowing the surface. Sprinkler systems should be turned off at least 24 hours before the scheduled sealing date and should not be running during or after the sealcoat is applied.
The pavement must also be free of any noticeable dirt or debris. This is why a thorough sweep and cleaning are needed before the project can begin. If rain is in the forecast, it may be necessary to postpone the project until the weather clears up.
Then, the workers can begin to apply the asphalt sealant. This is usually done with a spray or squeegee system that is either manual or self-propelled. A good squeegee system should be able to handle up to 1,000 square feet per hour. For larger areas, a hydraulic sprayer is more efficient. The finished product should be dark in color, creating a clean and attractive appearance to the parking lot or driveway.
Application
Before sealcoating can be applied, the pavement must be fully repaired. All cracks should be filled, potholes patched, and severely damaged areas replaced. It is also recommended that you remove any weeds growing on the blacktop. Once repairs have been completed, the pavement should be cleaned and sanded down to prepare it for the application process. Misting the pavement with water just prior to starting the application can temporarily lower its temperature, making it easier for the emulsion to bond with the surface.
The next step is to block off the area being coated and protect it from traffic, pets, and debris. It is also a good idea to turn off your sprinkler system if you have one, to prevent it from watering the newly-applied asphalt during the dry time that follows. Once the area has been blocked off, it is a good idea to clean any trash or debris from the parking lot, as well as wash away any oil stains that may have appeared on the surface.
Sealcoating acts as a protective layer for asphalt surfaces, shielding them from the elements, such as UV rays, harsh chemicals, and water intrusion, and it helps to prevent brittleness that occurs as asphalt ages. It can extend the lifespan of asphalt surfaces, significantly, and it can save significant costs in the long run.
Refined coal tar and asphalt emulsion sealcoats are typically supplied as concentrates that need to be mixed with water, silica sand and additives for proper application consistency according to the manufacturer’s recommended mix designs. Specialty surfactants and emulsifiers are used to keep the binder and filler particles properly dispersed in the wet state.
The mixture is applied to the pavement using a spray applicator or a brush and roller, with the amount of material being adjusted as needed for an even coat. It is important to note that the quality of the sealcoat depends on a number of factors, including the proper mixing and application, the ambient temperatures and humidity, and the thickness of the cured film. Sealcoating should be reapplied every few years to maintain optimal performance.
Drying
It’s important to allow the seal coating to dry fully before subjecting it to foot or vehicle traffic. This will ensure that the coat bonds well with the asphalt surface and provides maximum protection. Ideally, the surface should be left to dry for one to three days before allowing traffic on the area.
Humidity has a big impact on how quickly the material dries and cures. The higher the humidity level is, the longer it will take for the sealcoat to dry. Keeping humidity levels below 60 percent will help to hasten the drying process.
Once the sealcoat dries, it will feel hard and rigid to the touch. In order for the coating to fully cure, it will need to completely release any water or solvents. This is usually achieved through evaporation. The drier the coating is, the stronger it will be and the better its performance will be.
Some sealcoat manufacturers use additives that are designed to speed up the drying process in less than ideal weather conditions. These additives work well in warm weather conditions, but may not be effective if the temperature is too low or too high.
When working with any type of chemicals, it’s important to be cautious and follow all safety procedures. All workers should wear long sleeved shirts, pants, impervious boots and gloves, as well as protective eyewear and face masks. The equipment used in this process should also be carefully cleaned and thoroughly disinfected after every use. Coal tar sealants are especially hazardous and should only be handled by qualified professionals.
A properly done sealcoat will make the asphalt surface look brand new and protect it from damage. It will also help to extend the life of the pavement and reduce maintenance costs. However, if the sealcoating is not fully dried, it can be subjected to premature wear and tear that can lead to cracking or scuffing.
Taking the time to prepare the area, block off parking lots and hire professional sealcoat contractors are essential steps in the application process. However, if the time and money savings are too great to resist, many owners choose to apply their own sealcoat. While this does give them complete control over the project, it can be risky and result in inferior quality.